Selection of Traverse Unit
Side Thrust : This represents the maximum force that can be safely applied. If the force exceeds this value, the unit may slip.
Pitch : Pitch is the linear movement of the traverse unit for one rotation of the shaft. It is adjustable using the dial.
Adjusting the Pitch : To adjust the pitch, press the pointer lever down and shift it along the dial for pitch variation.
Linear Speed : The linear speed depends on the shaft speed and pitch setting.
Shaft Speed : Shaft speed is calculated in relation to the maximum pitch of the traverse unit and the maximum linear speed required.
Recommended Shaft Speed = Max Linear Speed Required / (0.9 × Maximum Pitch of Traverse Unit Selected)
Spooling Application : In spooling applications, drive to the traverse shaft is provided from the bobbin drive shaft to ensure automatic synchronization of speed. Maintain the speed ratio between the bobbin drive and traverse shafts for precise pitch adjustments.
Speed Ratio (dr/ds) = 0.90 × Maximum Pitch of Traverse Unit / Maximum Pitch Required for the Application
- dr = Diameter of Pulley or Number of Teeth on Traverse Shaft
- ds = Diameter of Pulley or Number of Teeth on Bobbin Drive Shaft
Where:
Refer to Figure 16 for visual representation.
Layer Winding Application : Speed ratio is calculated based on the maximum width or diameter of the material.
Speed Ratio (dr/ds) = 0.90 × Maximum Pitch of Traverse Unit / Maximum Diameter or Width of Material
Ensure that the bolt length used for mounting guide assemblies doesn't exceed the maximum insertion depth to avoid issues. Exceeding the specified value (N) may lead to the unit not reversing at the end limits, a slowdown in operation, different pitches for forward and reverse directions, and potential damage to the reversal plate.
Refer to Figure 17 for the maximum insertion depth for various models.
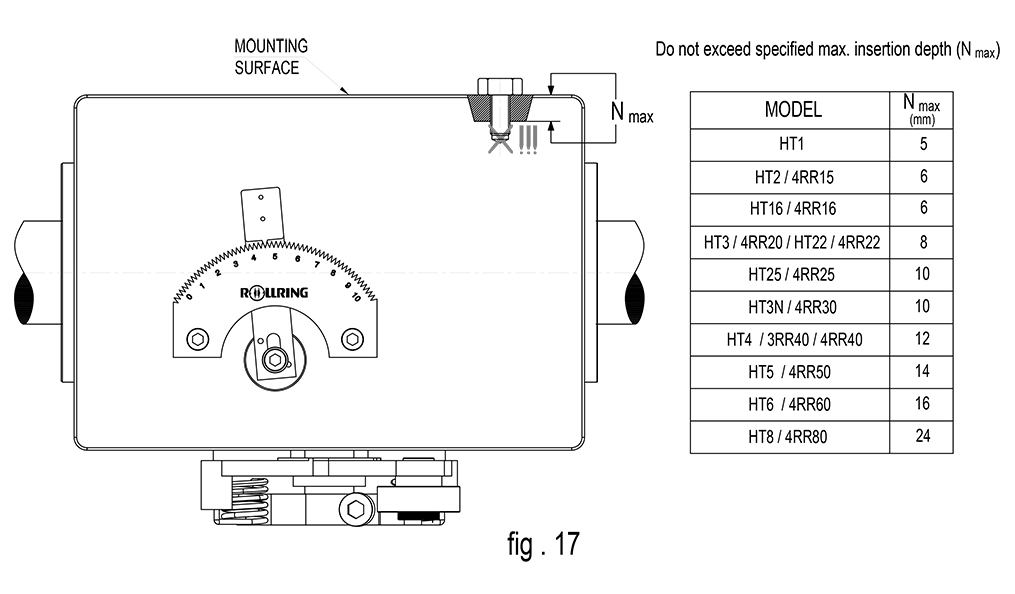
- Assemble the traverse unit onto the shaft through shaft rotation.
- Set the pitch to the maximum setting.
- Insert one end of the shaft into the traverse unit and rotate the shaft.
- To remove the traverse unit, simply rotate the shaft in the reverse direction. Note: Chamfer the shaft end to 2X 300 to prevent damage to the Rolling Rings during installation.
Reversal Time:
Instantaneous and automatic, depends on linear speed.
Refer Fig 18 for reversal time at various settings.
By default, Traverse units are typically configured for clockwise rotation of the shaft, unless specific requirements dictate otherwise. Here are two common orientations with explanations and visual references
Top Towards (Clockwise Rotation) : In this configuration, the Traverse unit is set up with the bearing on the reversal lever pointing towards the speed setting dial position. This aligns with the default clockwise rotation of the shaft.
Refer to Figure 19 for a visual representation.
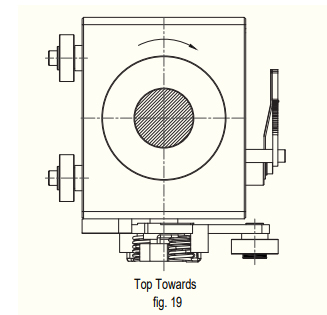
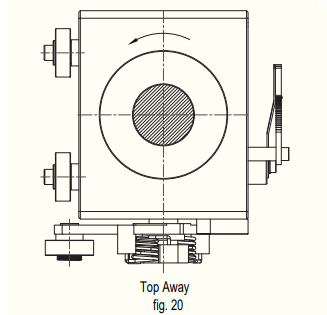
Top Away (Anti-Clockwise Rotation) : For anti-clockwise rotation of the shaft, the Traverse unit is configured differently. In this case, the bearing on the reversal lever is positioned away from the speed setting dial, accommodating the anti-clockwise rotation of the shaft.
Refer to Figure 20 for a visual representation.
Ensure the correct orientation during installation to match the desired rotation direction of the Traverse unit. This information, along with the accompanying photos and drawings, should guide the proper setup and alignment for your specific application.
Easily switch between clockwise and anticlockwise rotation by altering the reversal mechanism's position without opening the unit. Follow these steps:
To modify the Traverse unit from clockwise to anticlockwise direction of shaft rotation, or vice versa, you can follow these straightforward steps. This alteration involves adjusting the position of the Reversal mechanism without the need to open the unit. Please adhere to the instructions below for a smooth modification.
- Remove the Release Lever: Loosen the bolt to detach the Release lever.
- Remove Springs and Reversal Lever: Carefully take out the springs and the Reversal Lever.
- Remove Striker Plate: Detach the Striker Plate from its current position.
- Refit Striker Plate on Opposite Side: Mount the Striker Plate on the opposite side from where it was originally positioned.
- Refit Reversal Lever with a 180° Turn: Reattach the Reversal Lever after turning it by 180 degrees
- Reassemble Springs and Release Lever: Put the Springs and Release Lever back in place. Ensure that the lugs of the springs are not bent. Insert the long lug of the spring into the Reversal Lever and the short lug into the Release lever.
- Operate Reversal Lever Manually: Manually operate the Reversal lever and listen for the knocking sound.
With these modifications completed, your Traverse unit will be ready to operate in the opposite direction of shaft rotation as desired. Follow these instructions accurately for a successful conversion of the Traverse unit's rotation direction without any complications.
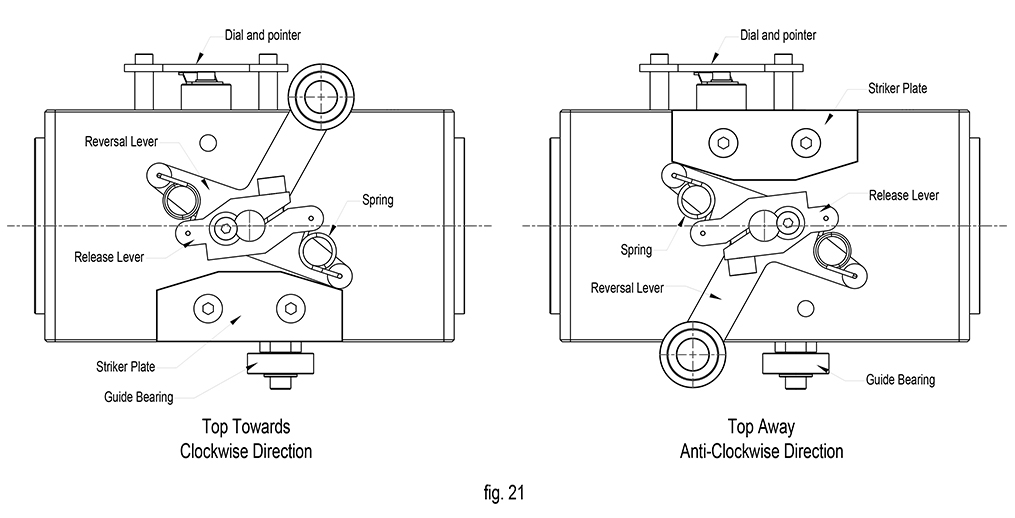
Refer to Figure 21 for a visual guide.
Always follow the manufacturer's guidelines and instructions for proper usage and modification.
Download Catalogue